BASF & Essentium: Die 3D-gedruckte Prothese
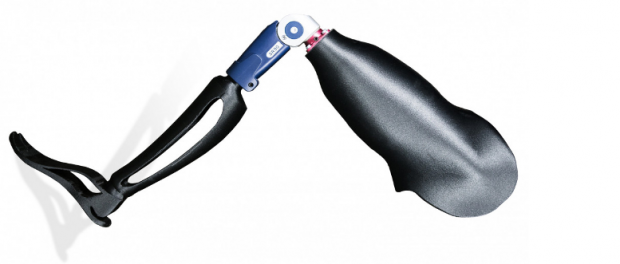
Die Unternehmen >>BASF<< und >>Essentium<< haben in Kooperation durch Zuhilfenahme eines 3D-Druckverfahrens eine Beinprothese hergestellt. Aufgrund von 3D-Scannern können damit passgenaue Prothese angefertigt werden.
„Der Chemie-Gigant BASF hat zusammen mit Essentium eine 3D-gedruckte Beinprothese entwickelt. Diese soll durch den Einsatz von Druckmaterial mit Carbonfasern höchsten Beanspruchungen standhalten. Erst vor wenigen Tagen hat BASF neue Filamente angekündigt. Wenig überraschend ist es daher, dass jetzt auch die ersten Anwendungen für diese neuen Materialien bekannt werden. Bei der neuen 3D-gedruckten Prothese soll es sich um die mechanisch stabilste 3D-gedruckte Beinprothese auf dem Markt handeln (die mit dem schon bekannten Ultramid Material hergestellt wird).“
„Chris Casteel hat mit seinen Patienten zusammengearbeitet, um die 3D-Prothese zu testen und Essentium und BASF in Echtzeit über Verbesserungen bei der Materialauswahl und des 3D-Druckprozess informiert. Den Aussagen der Patienten zufolge, sind die Fassungen komfortabler und passen perfekt, heißt es auf der Website weiter. Dabei haben Essentium und BASF die strengen Standardrichtlinien für additive Fertigung sorgfältig eingehalten.“